Riciclo auto, prima era marketing, ora è necessità: intervista con RadiciGroup
Il gruppo ha portato avanti un progetto per riciclare le componenti delle vecchie auto.
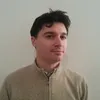
Il tema del riciclo sta diventando sempre più importante nel mondo automotive. Le case automobilistiche, infatti, sono tutte impegnate a sviluppare nuovi sistemi per riutilizzare le materie prime alla base di alcune componenti giunte a fine vita e, in generale, a ridurre le emissioni inquinanti. Si pensi, per esempio, a quanto si sta facendo con le batterie delle auto elettriche. Tuttavia, il lavoro non si ferma solo agli accumulatori, ma riguarda anche molte altre parti dei veicoli e, potenzialmente, le vetture nella loro interezza.
Per arrivare a rendere davvero protagonista l'industria automotive nel campo dell'economia circolare, c'è però bisogno di fare un grande lavoro che deve partire sin dalla progettazione delle vetture. Solo in questo modo sarà possibile realizzare modelli con componenti già strutturati per poter essere recuperati facilmente. Si tratta di argomenti complessi ed interessanti di cui sentiremo sicuramente parlare molto nel corso dei prossimi anni.
Proprio per questo, abbiamo voluto approfondire queste tematiche con Cesare Clausi, Global Sales Director di RadiciGroup High Performance Polymers, la divisione di RadiciGroup specializzata nella produzione e commercializzazione di tecnopolimeri per uso ingegneristico (a base poliammide, poliestere e altri materiali). Presente su scala mondiale, grazie a un network commerciale dislocato in tutti i continenti e a un’attività di ricerca e sviluppo globale, la divisone è parte di RadiciGroup multinazionale attiva anche nei settori della chimica e delle soluzioni tessili avanzate.
I prodotti dell’area High Performance Polymers di RadiciGroup trovano applicazione principalmente nei seguenti settori: automotive, elettrico-elettronico, water management, beni di consumo e industriale.
PROGETTO CAR E-SERVICE
RadiciGroup High Performance Polymers ha partecipato al progetto Car E-Service finanziato dal programma quadro dell'Unione Europea per la ricerca e l'innovazione Horizon 2020. Obiettivo? Quello di sviluppare modelli innovativi di economia circolare per l’industria automotive. E in particolare RadiciGroup si è occupata di recuperare componenti in poliammide provenienti dalle auto a fine vita trasformandoli, a seguito di una serie di formulazioni e processi, in una nuova materia prima a base polimerica. Grazie a Cesare Clausi, abbiamo, dunque, potuto sapere qualcosa di più del progetto, di come avviene la scelta delle parti da riutilizzare, della fase di riciclo vera e propria e della "seconda vita di queste componenti".
Clausi ci spiega che il compito di RadiciGroup era quello di creare un esempio concreto di economia circolare grazie alla grande esperienza del Gruppo nel settore dei tecnopolimeri , anche da riciclo. Sono stati, dunque, individuati dei componenti specifici guardando innanzitutto alla facilità di reperimento. Oltre a questo, si è puntato anche alla natura omogenea della loro matrice polimerica. Per esempio, un airbag è composto quasi interamente da poliammide 66. Dunque, una volta rimosso dall'auto a fine vita può essere trattato senza complicazioni date da "inquinanti" che in altri componenti, invece, si possono trovare.
La rimozione di un airbag è un'operazione relativamente semplice ma bisogna prestare una certa cautela e deve essere fatta da specialisti e quindi c'è anche il tema della collaborazione con chi conosce bene le attività di smantellamento. Restando sugli airbag, si è fatto in modo che scoppiassero nell'auto, liberando il gas. Poi si è provveduto a rimuoverli e a raccoglierli separatamente. L'aspetto della raccolta diventa più importante nel caso, per esempio, dei copriruota perché possono essere fatti di poliammide 6, 66 o di polipropilene rinforzato. Una volta separati e raccolti questi airbag, li abbiamo mandati a "macinare". La macinazione non la facciamo al nostro interno ma presso aziende specializzate terze oppure presso uno dei nostri siti produttivi che si occupa del riciclo.
Il Global Sales Director di RadiciGroup High Performance Polymers aggiunge poi che, una volta ricevuto il "macinato", si occupano internamente di "caratterizzarlo", cioè di fare un'analisi chimico-fisica di queste materie prime in ingresso andando a vedere il tipo della matrice polimerica presente. Clausi ci spiega anche che prima di avviarle al processo di trasformazione che riguarda l'estrusione e che viene effettuato internamente, viene deciso in cosa trasformare questo prodotto.
Dobbiamo partire dalle caratteristiche in ingresso delle materie prime, capire se possono essere adatte per ottenere dei tecnopolimeri con determinate prestazioni. Guardiamo già all'utilizzo finale. Quando parliamo di prestazioni di un nostro prodotto finito dobbiamo guardare non solo alle caratteristiche chimico-fisiche che riguardano, per esempio, il punto di fusione, ma soprattutto alle caratteristiche meccaniche.
Le applicazioni principali della poliammide nell'auto stanno nel sottocofano e quindi vicino al motore a combustione; è facile immaginare le temperature e le sollecitazioni.
Clausi aggiunge che a quel punto si individuano le proprietà obiettivo da raggiungere e si decide come costruire una formulazione o modificare in fase di estrusione queste materie prime per arrivare ai risultati desiderati. Semplificando, la poliammide ottenuta a partire dal recupero degli airbag viene fusa, e additivata con rinforzi in fibra di vetro o altro, con l'obiettivo di migliorarne le proprietà di stabilità termica e le performance tecniche in generale.
Il materiale esce poi dal processo di estrusione in forma di spaghetti che vengono sminuzzati in granuli. Rispetto a come erano entrate, queste materie prime seconde escono con caratteristiche differenti. Alla fine, vengono misurate nuovamente le proprietà per verificare se corrispondono agli obiettivi che erano stati prefissati. A quel punto, il materiale è pronto ad essere venduto e nuovamente trasformato in un manufatto plastico da altre aziende più a valle.
Nell'ambito del progetto Car E-Service, il Gruppo ha identificato nuove possibili applicazioni dei tecnopolimeri da riciclo. Per esempio, sono stati trasformati in un componente di una colonnina per la ricarica delle auto elettriche o utilizzati per realizzare prodotti come spine e prese.
Nello stesso progetto abbiamo anche utilizzato le materie prime ottenute dagli airbag per creare componenti che però servivano a noi per validarne le proprietà. Ci siamo costruiti nel tempo dei pezzi stampati che ci servivano per capire le principali caratteristiche di un materiale (dimostratori).
Un lavoro che è stato fatto, ci è stato spiegato, anche per le materie prime ricavate dai copricerchi, dalle maniglie e dai tergicristalli. Un grande apporto a tutto questo processo lo ha dato il servizio di progettazione interna che ha lavorato alla simulazione del comportamento di questi materiali riciclati per verificare con un buon grado di certezza che sarebbero stati in grado di ottenere gli stessi risultati di un prodotto ottenuto a partire da un polimero "vergine".
TRASPORTO E CONSERVAZIONE
Ma come si conservano questi prodotti e come si spediscono alle aziende che ne hanno bisogno? Su questi temi, Clausi è stato molto chiaro. La poliammide ha una caratteristica molto importante e cioè quella di assorbire molta l'umidità. Per questo, va mantenuta più secca possibile. In caso contrario, ci possono essere problemi quando viene ritrasformata in un qualche pezzo. Vengono dunque utilizzati dei silos con umidità controllata. Ci sono poi diverse forme di confezionamento. C'è, per esempio, il sacco da 25 kg alluminato con una protezione in polipropilene che viene garantito per 6 mesi.
In alternativa, sono disponibili imballi chiamati "octabin" che contengono 1.000 kg di materiale. Poi ovviamente molto dipende anche da dove bisogna trasportarlo.
ABBATTIMENTO DELLE EMISSIONI
Legato strettamente al tema del riciclo c'è anche quello della riduzione delle emissioni inquinanti, un aspetto su cui le aziende del settore automotive stanno lavorando molto. Clausi ci spiega che il grosso dell'impatto ambientale avviene nella fase a monte, dall'estrazione del petrolio alla raffinazione dell'industria chimica.
Quando parto da un prodotto che non richiede un nuovo ciclo dalla nascita, cioè dall'estrazione e poi dalla trasformazione, ma che parte da un qualcosa che è arrivato a fine vita o è uno scarto di produzione di altri cicli come quello tessile o delle polimerizzazioni, sto già partendo tagliando il grosso della fetta dell'impatto di quel prodotto. Quando facciamo dei confronti sull'impatto ambientale mettendo a confronto un polimero vergine con un polimero che arriva da un riciclo industriale, l'abbattimento arriva anche all'80%.
LA COLLABORAZIONE CON I COSTRUTTORI
Il progetto Car E-Service della durata di tre anni si è appena concluso. Dunque, abbiamo chiesto cosa il gruppo ha imparato e come sfrutteranno l'esperienza accumulata. Clausi ha voluto sottolineare che hanno imparato molto. Partendo dal fatto che la Business Area High Performance Polymers ha una lunga esperienza nel recupero e nel riciclo di materiali polimerici, Car E-Service è stato il primo progetto nell'ambito automotive di una certa importanza che ha permesso di fare squadra tra attori della filiera.
Guardiamo al lavoro fatto sugli airbag come qualcosa che possiamo davvero consolidare e da cui far partire uno sviluppo, un circolo virtuoso che si possa tradurre poi in un business regolare che in un certo senso renda sistematico anche il recupero degli airbag per poi essere incanalati nel riciclo dei nostri prodotti.
Clausi ovviamente spiega che è necessario stringere delle partnership. Poi c'è un aspetto importante che va a "pesare" molto sull'intero processo e cioè che è fondamentale partire dalla progettazione dei componenti tenendo conto di come si potranno recuperare a fine vita. I costruttori, dunque, dovrebbero pensare a realizzare auto con parti riciclabili o che possano essere disassemblate velocemente e avviate facilmente al recupero.
Stiamo dando le carte d'identità dei nostri prodotti in termini di impatto ambientale. Agli uffici di progettazione dei costruttori di auto forniamo la dichiarazione ambientale del nostro prodotto.
Le case automobilistiche possono quindi confrontarla con altri prodotti per scegliere il migliore e assicurare il minor impatto ambientale possibile. Il metal replacement è un tema molto importante per tutti i costruttori di auto: sostituire componenti di metallo con altre realizzate in materiale polimerico è una scelta che porta vantaggi in termini di emissioni nell'intero ciclo di vita perchè alleggerisce l'auto, un dettaglio non di poco conto soprattutto sulle elettriche che, a causa del pacco batteria, pesano di più delle endotermiche.
Oltre alla riduzione di peso, c'è anche una maggiore libertà di progettazione dei componenti. Se fino a 10 anni fa i costruttori utilizzavano i prodotti riciclati per una questione di marketing, oggi non è più così. Richiedere ad un produttore un tecnopolimero che sia in parte o del tutto riciclato, permette alle case automobilistiche di poter calcolare la riduzione delle emissioni di CO2 per l'intero ciclo di vita dell'auto.
APPLICAZIONI NEL MONDO AUTOMOTIVE
L'avvento della mobilità elettrica, ci ha spiegato Clausi, ha rappresentato una sfida per il gruppo visto che i prodotti per il mondo automotive, sino ad ora, erano stati pensati per le auto endotermiche. Una sfida che si è dimostrata relativa in quanto si è trattato di guardare il cambiamento in maniera positiva utilizzando le conoscenze del gruppo per inserirsi in questo nuovo contesto.
Si sono, infatti, aperte nuove possibilità. Per esempio, le elettriche dispongono di grandi batterie ed è necessario garantire l'isolamento dei cavi. Servono anche prodotti con una conducibilità termica differente e dotati di proprietà di autoestinguenza. Se brucia un componente di un'auto elettrica, spiega Clausi, bisogna fare in modo che poi si spenga nel minor tempo possibile.
Un lavoro che il gruppo ha potuto intraprendere grazie anche alle specifiche competenze già sviluppate da tempo in mercati come l'industria elettrica/elettronica e l'ingegneria civile/industriale.
Quello che si temeva di perdere in termini di volumi e di vendita sarà possibile recuperarlo in altre applicazioni. Si pensi, per esempio, alla connettoristica, ai separatori delle celle delle batterie, ai circuiti di raffreddamento, alle coperture dei cavi ed altro.